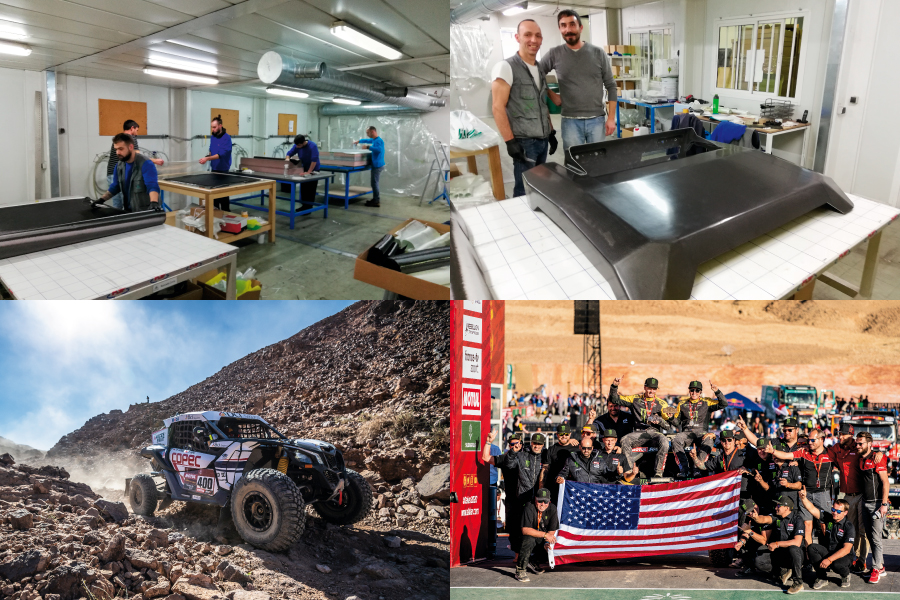
After contacts and a presentation visit that was achieved with the help of a friend who is a pilot in the all-terrain race world, we were contacted in the beginning of November to present a proposal to make 2 references (left piece + right piece) in fiber carbon for a new Can-Am that would run on the Dakar. We were told from the first contact that the deadline was critical and we would have to commit to the agreed dates, there could be no delays because on the 22nd December the cars would have to leave for the RACE, so the next day the proposal was sent and 2 days later the PO came.
So the first race started.
Define specifications, develop process, design moulds, buy materials, machine moulds, finish and make 1 + 1 prototypes to validate the client 7 days after the PO. Approved prototypes, we can produce 9 + 9 parts, each part takes 8 hours to produce by manual lay-up process using vacuum infusion, as we have 2 moulds it’s 9 working days, perfect warm-up.
Fortunately, when we went to the customer to validate the first prototypes, he showed us another piece and launched us another challenge: “… and what about this part can it be done within the same deadline?”. Right there we defined the specifications and requirements to be fulfilled for this 3rd part. We asked them to send us the CAD of the part and we asked for a day to plan and evaluate if we would be able to do it.
In fact, this part which is the Roof of the Can-Am, due to its dimensions (1600x1400x300mm) we had to take care of materials and resources that would allow us to elaborate a feasible planning and only after 4 days we presented the proposal and the execution plan.
On 20th Nov we received the order to make these parts and at this stage with the execution of the first 2 references very advanced, we started to develop the process, design moulds, buy materials, machine moulds, surface finishing and prototype to validate the Roof on the client 13 days after PO.
Approved prototype. We can produce 8 pieces, each piece takes 16h to produce, if everything goes well, there are 8 working days, making the lay-up and infusion during the day and curing during the night, at least this was the plan that did not occur in such a linear way.
During the process of developing the Roof mould, the client makes an RFQ for another part called Top Scoop that mounts on the Roof, although this part was not as big as the Roof, it was geometrically more challenging and with more complex finishing operations.
At this moment we had to gather the composites team, in order to be able to commit to this fourth reference, we had to define a strategy to have more resources because we were already working 12 hours a day and would not be enough to make this piece before the maximum period of 22nd Dec. We decided that if we won this reference we would strengthen the team with people from the metal division who have already supported us and have some experience and we identified 2 other technicians who work in another company with whom we have relations, who have a lot of experience and can help if necessary, the team also committed to work on the weekends to complete the goal.
We made the proposal and production planning and send it to the client, 2 days later the PO came and with this 4th reference we started to assume a high risk for meeting the client's deadline. Nine days later on 6th Dec we presented the first Top Scoop prototype to the customer and it was approved for production.
We had 8 pieces to produce with a cycle time of 14h in parallel with the Roofs, we started immediately with the plan previously defined and we reinforced the team with 2 more persons, we started working in 2x 12h shifts and we didn't stop from 6 to 20 December. In order to optimize operations, we decided to make infusions and cures on all the parts and only after they were all done, we made the cuts and finishes.
From the 14th to the 21st of December we had 2 external collaborators who helped us at the weekend and during the week from 18h to 3h in the morning, this help was precious for the execution of the cuts and finishes of the pieces.
On December 16 the client consulted us to make some side covers, the first reaction was to refuse but after seeing the drawings we realized that moulds were not required, as they were flat parts and if we resorted to water jet cutting, it also did not interfere with the cuts and finishes that was where the pressure was in those last days, so we presented a proposal and the client awarded 8 + 8 side covers 4 days before the deadline.
On the 20th, 21st and 22nd of December we managed to deliver all the pieces that we committed, there was a Roof in which the infusion was not perfect and we had to repeat this part, however we achieved all the objectives that we set ourselves, delivering all the references on time and with the desired quality. It was a challenging race where we rested between cures, redefined plans and dealt with the adversity of sometimes not running as expected.
This is only possible with great teamwork, with a lot of commitment and dedication from the most novice collaborator to the decision makers, collaborating very closely with the client to obtain feedback, validate and correct deviations from the plan in an immediate way.
The Dakar has 12 stages, our project had these:

In short, we industrialized 6 references, made 4 moulds and produced 52 parts of carbon fiber in 6 weeks.
Congratulations to Newstamp Composites, we are winners.
Pedro Santos